Destylacja rozpuszczalników to proces, który ma na celu oddzielenie substancji na podstawie różnic w ich temperaturach wrzenia. Jest to technika szeroko stosowana w chemii oraz przemyśle, szczególnie w produkcji i oczyszczaniu różnych związków chemicznych. Proces ten polega na podgrzewaniu cieczy do momentu, w którym zaczyna parować, a następnie schładzaniu pary, aby skondensować ją z powrotem do stanu ciekłego. W wyniku tego procesu można uzyskać czystszy produkt, ponieważ różne substancje mają różne temperatury wrzenia. Na przykład, jeśli mamy mieszaninę wody i alkoholu, to alkohol będzie parował w niższej temperaturze niż woda, co pozwala na jego oddzielenie. Destylacja może być przeprowadzana na różne sposoby, w tym destylację prostą oraz destylację frakcyjną, która jest bardziej skomplikowana i pozwala na separację wielu składników jednocześnie.
Jakie są zastosowania destylacji rozpuszczalników w przemyśle
Zastosowania destylacji rozpuszczalników są niezwykle szerokie i obejmują wiele branż przemysłowych. W przemyśle chemicznym destylacja jest kluczowym procesem wykorzystywanym do oczyszczania surowców oraz produkcji różnych substancji chemicznych. Na przykład, w produkcji alkoholi etylowych destylacja pozwala na uzyskanie wysokiej czystości spirytusu, który jest używany zarówno w przemyśle spożywczym, jak i farmaceutycznym. W branży petrochemicznej destylacja frakcyjna jest stosowana do separacji różnych frakcji ropy naftowej, co umożliwia produkcję benzyny, oleju napędowego oraz innych paliw. Ponadto destylacja znajduje zastosowanie w laboratoriach analitycznych, gdzie służy do oczyszczania reagentów oraz przygotowywania próbek do badań. W przemyśle kosmetycznym destylacja jest wykorzystywana do pozyskiwania olejków eterycznych z roślin, co pozwala na tworzenie naturalnych kosmetyków o wysokiej jakości.
Jakie są rodzaje destylacji rozpuszczalników i ich różnice
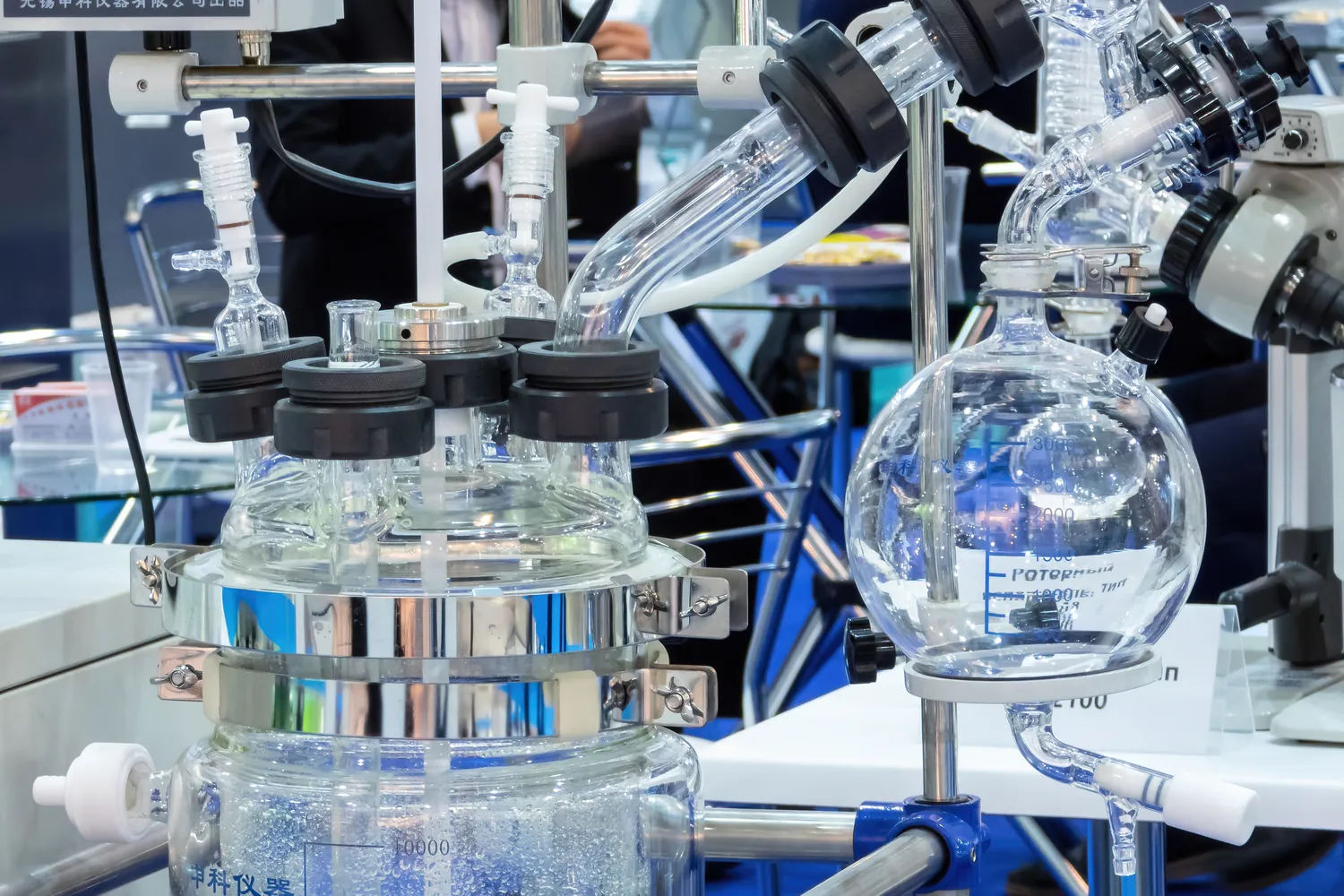
W kontekście destylacji rozpuszczalników wyróżniamy kilka głównych rodzajów tej techniki, z których każdy ma swoje specyficzne zastosowania oraz zalety. Destylacja prosta jest najprostszym rodzajem tego procesu i polega na podgrzewaniu cieczy do momentu jej wrzenia oraz zbieraniu pary, która następnie kondensuje się w chłodnicy. Jest to skuteczna metoda dla mieszanin zawierających substancje o znacznie różnych temperaturach wrzenia. Z kolei destylacja frakcyjna jest bardziej zaawansowaną techniką, która wykorzystuje kolumny frakcyjne do separacji składników o zbliżonych temperaturach wrzenia. Dzięki temu możliwe jest uzyskanie czystszych frakcji oraz lepsza kontrola nad procesem separacji. Innym rodzajem jest destylacja azeotropowa, która służy do oddzielania składników tworzących azeotropy – mieszaniny o stałym składzie, które nie zmieniają się podczas destylacji.
Jakie są korzyści z wykorzystania destylacji rozpuszczalników
Wykorzystanie destylacji rozpuszczalników niesie ze sobą wiele korzyści zarówno dla przemysłu, jak i dla laboratoriów badawczych. Przede wszystkim proces ten pozwala na uzyskanie wysokiej czystości produktów chemicznych, co jest kluczowe w wielu aplikacjach przemysłowych oraz badawczych. Czyste substancje są niezbędne do dalszych reakcji chemicznych oraz produkcji wyrobów końcowych o wysokiej jakości. Dodatkowo destylacja umożliwia efektywne odzyskiwanie cennych surowców z odpadów lub nieczystości, co przyczynia się do zmniejszenia kosztów produkcji oraz ochrony środowiska. Kolejną zaletą jest możliwość skalowania procesu – od małych instalacji laboratoryjnych po duże zakłady przemysłowe, co sprawia, że technika ta może być dostosowana do różnych potrzeb produkcyjnych.
Jakie są wyzwania związane z destylacją rozpuszczalników
Pomimo licznych korzyści, destylacja rozpuszczalników wiąże się również z pewnymi wyzwaniami, które mogą wpływać na efektywność i koszty procesu. Jednym z głównych problemów jest konieczność precyzyjnego kontrolowania temperatury, ponieważ niewłaściwe ustawienia mogą prowadzić do niepełnej separacji składników lub ich degradacji. W przypadku mieszanin o zbliżonych temperaturach wrzenia, takich jak woda i alkohol, proces destylacji może być szczególnie trudny i wymaga zastosowania bardziej zaawansowanych technik, takich jak destylacja frakcyjna. Kolejnym wyzwaniem jest zarządzanie dużymi ilościami energii potrzebnej do podgrzewania cieczy oraz chłodzenia pary. Wysokie koszty energii mogą znacząco wpłynąć na rentowność procesu, dlatego wiele zakładów poszukuje sposobów na optymalizację zużycia energii poprzez zastosowanie nowoczesnych technologii oraz systemów odzysku ciepła. Dodatkowo, w przypadku pracy z substancjami toksycznymi lub łatwopalnymi, konieczne jest zachowanie szczególnych środków ostrożności oraz przestrzeganie rygorystycznych norm bezpieczeństwa, co może zwiększać koszty operacyjne.
Jakie są nowoczesne technologie w destylacji rozpuszczalników
W ostatnich latach rozwój technologii w dziedzinie destylacji rozpuszczalników przyniósł wiele innowacyjnych rozwiązań, które zwiększają efektywność i bezpieczeństwo tego procesu. Jednym z takich rozwiązań jest zastosowanie kolumn frakcyjnych o wysokiej wydajności, które pozwalają na lepszą separację składników o zbliżonych temperaturach wrzenia. Dzięki nowoczesnym materiałom i konstrukcjom kolumn możliwe jest osiągnięcie znacznie wyższej czystości produktów końcowych. Innowacje obejmują także automatyzację procesów destylacyjnych, co pozwala na lepsze monitorowanie i kontrolowanie warunków pracy. Systemy automatycznego sterowania umożliwiają szybkie reagowanie na zmiany w procesie oraz minimalizują ryzyko błędów ludzkich. Ponadto rozwijają się technologie związane z odzyskiem energii, takie jak systemy kogeneracyjne czy pompy ciepła, które pozwalają na zmniejszenie kosztów operacyjnych poprzez efektywne wykorzystanie energii cieplnej.
Jakie są różnice między destylacją a innymi metodami separacji
Destylacja to jedna z wielu metod separacji substancji chemicznych, jednak różni się ona od innych technik zarówno pod względem zasad działania, jak i zastosowań. Na przykład ekstrakcja jest metodą opartą na różnicach w rozpuszczalności składników w różnych rozpuszczalnikach. W przeciwieństwie do destylacji, która polega na wykorzystaniu różnic w temperaturze wrzenia, ekstrakcja często wymaga użycia dodatkowych substancji chemicznych do oddzielania składników. Inną popularną metodą separacji jest filtracja, która polega na oddzielaniu cząstek stałych od cieczy lub gazu za pomocą porowatych materiałów filtracyjnych. Filtracja jest skuteczna w przypadku mieszanin zawierających cząstki stałe, ale nie sprawdza się w przypadku cieczy o podobnych właściwościach fizykochemicznych. Chromatografia to kolejna technika separacyjna, która wykorzystuje różnice w interakcjach między substancjami a fazą stacjonarną i mobilną. Jest to metoda bardzo precyzyjna i często stosowana w laboratoriach analitycznych do identyfikacji składników mieszanin.
Jakie są przyszłe kierunki badań nad destylacją rozpuszczalników
Przyszłość badań nad destylacją rozpuszczalników zapowiada się obiecująco dzięki rosnącemu zainteresowaniu innowacyjnymi technologiami oraz ekologicznymi rozwiązaniami. Naukowcy i inżynierowie koncentrują się na opracowywaniu bardziej efektywnych procesów destylacyjnych, które będą wymagały mniej energii oraz surowców. Jednym z kierunków badań jest rozwój nowych materiałów dla kolumn frakcyjnych oraz elementów chłodzących, które mogą poprawić wydajność procesu. Ponadto badania nad zastosowaniem nanotechnologii w destylacji mogą prowadzić do stworzenia bardziej efektywnych systemów separacyjnych. W kontekście ochrony środowiska coraz większą uwagę zwraca się na metody zielonej chemii, które mają na celu minimalizację negatywnego wpływu procesów przemysłowych na środowisko naturalne. Przykładem może być poszukiwanie alternatywnych rozpuszczalników o mniejszym wpływie na zdrowie ludzi i ekosystemy.
Jakie są najczęstsze błędy podczas przeprowadzania destylacji rozpuszczalników
Podczas przeprowadzania procesu destylacji rozpuszczalników można napotkać wiele pułapek i błędów, które mogą wpłynąć na jakość uzyskanego produktu końcowego oraz efektywność całego procesu. Jednym z najczęstszych błędów jest niewłaściwe ustawienie temperatury wrzenia lub ciśnienia roboczego urządzeń destylacyjnych. Zbyt wysoka temperatura może prowadzić do niepożądanych reakcji chemicznych lub degradacji substancji, natomiast zbyt niska temperatura może skutkować niepełną separacją składników. Kolejnym problemem jest niewłaściwe dobranie sprzętu do specyfiki danej mieszaniny – użycie kolumny frakcyjnej o niewłaściwej wydajności może prowadzić do obniżenia czystości produktu końcowego. Błędy w przygotowaniu próbki przed rozpoczęciem procesu również mogą mieć negatywny wpływ na wyniki – nieodpowiednia mieszanka lub obecność zanieczyszczeń mogą zaburzyć przebieg destylacji. Ważne jest także regularne monitorowanie parametrów procesu oraz przeprowadzanie konserwacji sprzętu, aby uniknąć awarii lub niespodziewanych przestojów produkcyjnych.
Jakie są kluczowe aspekty bezpieczeństwa podczas destylacji rozpuszczalników
Bezpieczeństwo podczas przeprowadzania procesów destylacyjnych jest niezwykle istotne ze względu na ryzyko związane z pracą z substancjami chemicznymi oraz wysokimi temperaturami. Kluczowym aspektem bezpieczeństwa jest zapewnienie odpowiedniej wentylacji w pomieszczeniu roboczym, aby uniknąć gromadzenia się szkodliwych oparów czy gazów. Pracownicy powinni być wyposażeni w odpowiednie środki ochrony osobistej, takie jak rękawice ochronne czy okulary zabezpieczające przed działaniem substancji chemicznych. Ważne jest także przestrzeganie procedur awaryjnych oraz znajomość lokalizacji sprzętu gaśniczego i apteczek pierwszej pomocy w przypadku wystąpienia incydentów. Regularne szkolenia dla personelu dotyczące zasad BHP oraz procedur postępowania w sytuacjach awaryjnych są kluczowe dla utrzymania wysokiego poziomu bezpieczeństwa w zakładzie produkcyjnym czy laboratorium badawczym.