Destylator przemysłowy to urządzenie, które służy do oddzielania składników mieszanin cieczy na podstawie różnic w ich temperaturach wrzenia. Proces ten jest kluczowy w wielu branżach, takich jak przemysł chemiczny, petrochemiczny czy spożywczy. Działanie destylatora opiera się na cyklu podgrzewania cieczy, parowania jej składników oraz skraplania powstałych par. W pierwszym etapie ciecz jest podgrzewana w zbiorniku, a następnie, gdy osiągnie odpowiednią temperaturę, zaczyna parować. Wytworzone pary są kierowane do kolumny destylacyjnej, gdzie następuje ich schłodzenie i kondensacja. W wyniku tego procesu uzyskuje się frakcje o różnej czystości i składzie chemicznym. Destylatory przemysłowe mogą mieć różne formy, od prostych jednostek laboratoryjnych po zaawansowane systemy ciągłe stosowane w dużych zakładach produkcyjnych.
Jakie są rodzaje destylatorów przemysłowych i ich zastosowanie
W przemyśle można spotkać różne rodzaje destylatorów, które różnią się zarówno konstrukcją, jak i przeznaczeniem. Najpopularniejsze typy to destylatory prostokątne, kolumnowe oraz wirówkowe. Destylatory prostokątne są najczęściej wykorzystywane w małych zakładach produkcyjnych, gdzie wymagane są niewielkie ilości destylatu. Ich budowa jest stosunkowo prosta i pozwala na łatwe zarządzanie procesem. Z kolei destylatory kolumnowe są bardziej zaawansowane technologicznie i wykorzystywane w dużych zakładach przemysłowych do produkcji wysokiej jakości substancji chemicznych oraz paliw. Dzięki swojej konstrukcji umożliwiają one wielokrotne skraplanie par, co zwiększa efektywność procesu. Destylatory wirówkowe natomiast znajdują zastosowanie w przemyśle spożywczym, gdzie wykorzystywane są do separacji olejków eterycznych czy aromatów z surowców naturalnych.
Jakie są kluczowe elementy budowy destylatora przemysłowego
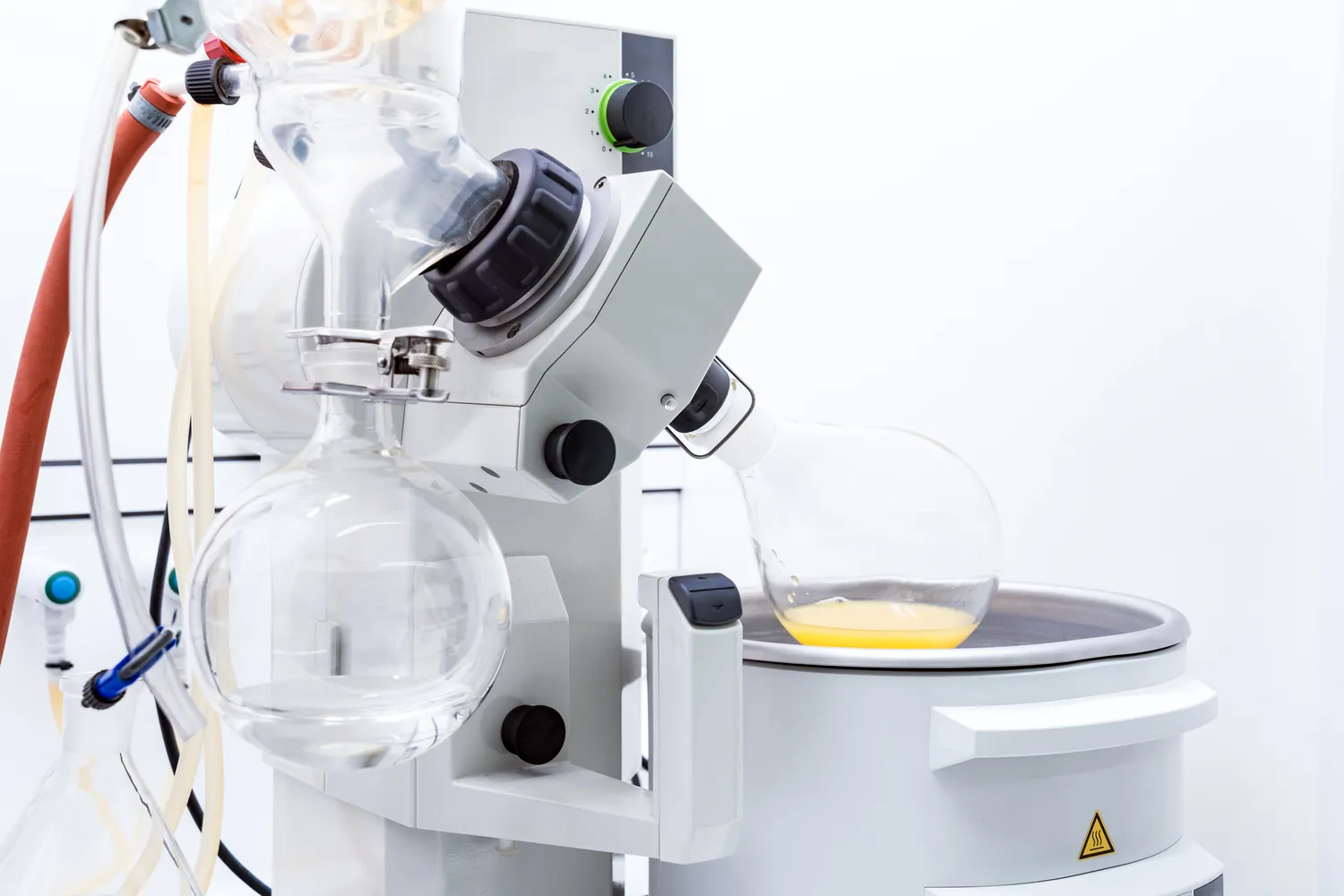
Budowa destylatora przemysłowego opiera się na kilku kluczowych elementach, które zapewniają jego prawidłowe działanie oraz efektywność procesu destylacji. Podstawowym komponentem jest zbiornik, w którym odbywa się podgrzewanie cieczy. Zbiornik ten musi być wykonany z materiałów odpornych na wysokie temperatury oraz korozję. Kolejnym istotnym elementem jest kolumna destylacyjna, która może mieć różną długość i średnicę w zależności od wymagań procesu. Wewnątrz kolumny znajdują się tzw. packingi lub talerze, które zwiększają powierzchnię kontaktu między parami a cieczą, co sprzyja efektywnemu rozdzielaniu składników. Następnie mamy skraplacz, który odpowiada za schładzanie par i ich kondensację do postaci cieczy. Ostatnim ważnym elementem jest system sterowania procesem, który monitoruje temperaturę oraz ciśnienie wewnątrz urządzenia, zapewniając optymalne warunki pracy.
Jakie są zalety stosowania destylatorów przemysłowych w produkcji
Stosowanie destylatorów przemysłowych w produkcji niesie ze sobą wiele korzyści, które przekładają się na efektywność oraz jakość procesów technologicznych. Przede wszystkim umożliwiają one precyzyjne oddzielanie składników mieszanin cieczy, co jest kluczowe dla uzyskania wysokiej jakości produktów końcowych. Dzięki zastosowaniu nowoczesnych technologii oraz automatyzacji procesów możliwe jest osiągnięcie dużej wydajności przy jednoczesnym obniżeniu kosztów produkcji. Destylatory pozwalają także na recykling surowców oraz minimalizację odpadów poprzez ponowne wykorzystanie niektórych frakcji w kolejnych procesach produkcyjnych. Dodatkowo nowoczesne destylatory charakteryzują się niskim zużyciem energii oraz wysoką efektywnością energetyczną, co wpływa na zmniejszenie śladu węglowego całego procesu produkcyjnego.
Jakie są wyzwania związane z obsługą destylatorów przemysłowych
Obsługa destylatorów przemysłowych wiąże się z szeregiem wyzwań technicznych oraz organizacyjnych, które mogą wpływać na efektywność całego procesu produkcyjnego. Przede wszystkim konieczne jest zapewnienie odpowiednich warunków pracy dla urządzeń, co obejmuje kontrolę temperatury oraz ciśnienia wewnętrznego. Niewłaściwe ustawienia mogą prowadzić do obniżenia jakości uzyskiwanego produktu lub nawet uszkodzenia sprzętu. Ponadto operatorzy muszą być dobrze przeszkoleni w zakresie obsługi urządzeń oraz znajomości procesów chemicznych zachodzących podczas destylacji. Inne wyzwanie to regularna konserwacja i serwisowanie urządzeń, które są niezbędne dla utrzymania ich sprawności oraz wydajności pracy. W przypadku awarii konieczne może być szybkie reagowanie i podejmowanie działań naprawczych, co wymaga odpowiednich zasobów ludzkich i technicznych.
Jakie są najnowsze technologie w destylacji przemysłowej
W ostatnich latach rozwój technologii destylacji przemysłowej przeszedł znaczną transformację, co pozwoliło na wprowadzenie innowacyjnych rozwiązań zwiększających efektywność i jakość procesów. Jednym z najważniejszych trendów jest automatyzacja, która umożliwia zdalne monitorowanie i kontrolowanie parametrów pracy destylatorów. Dzięki zastosowaniu zaawansowanych systemów informatycznych oraz czujników, operatorzy mogą na bieżąco śledzić zmiany temperatury, ciśnienia czy przepływu, co pozwala na szybką reakcję w przypadku nieprawidłowości. Kolejną nowinką technologiczną są destylatory membranowe, które wykorzystują specjalne membrany do separacji składników. Te urządzenia charakteryzują się wysoką efektywnością energetyczną oraz możliwością pracy w niższych temperaturach, co jest korzystne dla wielu procesów chemicznych. Warto również wspomnieć o zastosowaniu nanotechnologii w budowie elementów destylatorów, co pozwala na poprawę ich wydajności oraz odporności na korozję.
Jakie są koszty eksploatacji destylatorów przemysłowych
Koszty eksploatacji destylatorów przemysłowych są kluczowym czynnikiem wpływającym na rentowność procesów produkcyjnych. Wśród głównych kosztów można wyróżnić wydatki związane z energią, surowcami oraz konserwacją urządzeń. Koszt energii jest jednym z największych wydatków związanych z działaniem destylatora, ponieważ proces podgrzewania cieczy wymaga znacznych ilości energii cieplnej. Dlatego wiele zakładów inwestuje w technologie zwiększające efektywność energetyczną, takie jak odzysk ciepła czy zastosowanie odnawialnych źródeł energii. Kolejnym istotnym elementem kosztów są surowce wykorzystywane w procesie destylacji. W zależności od rodzaju produkcji oraz jakości surowców, koszty te mogą się znacznie różnić. Warto również uwzględnić wydatki na regularną konserwację i serwisowanie urządzeń, które są niezbędne dla utrzymania ich sprawności oraz wydajności pracy. W przypadku awarii konieczne mogą być dodatkowe koszty naprawy lub wymiany uszkodzonych komponentów.
Jakie są zastosowania destylatorów przemysłowych w różnych branżach
Destylatory przemysłowe znajdują szerokie zastosowanie w wielu branżach, co sprawia, że są one niezwykle ważnym elementem współczesnej produkcji. W przemyśle chemicznym służą do separacji różnych substancji chemicznych, co umożliwia uzyskanie wysokiej jakości reagentów i produktów końcowych. W branży petrochemicznej destylacja jest kluczowym procesem przy produkcji paliw, takich jak benzyna czy olej napędowy, gdzie oddziela się poszczególne frakcje ropy naftowej. Destylatory mają także swoje miejsce w przemyśle spożywczym, gdzie wykorzystywane są do ekstrakcji olejków eterycznych oraz aromatów z surowców naturalnych. Dzięki temu możliwe jest uzyskanie wysokiej jakości produktów spożywczych o intensywnym smaku i zapachu. Ponadto destylatory znajdują zastosowanie w produkcji alkoholi, gdzie proces fermentacji i destylacji pozwala na uzyskanie trunków o pożądanej mocy i smaku.
Jakie są kluczowe czynniki wpływające na wybór odpowiedniego destylatora
Wybór odpowiedniego destylatora przemysłowego to kluczowy krok dla zapewnienia efektywności procesów produkcyjnych oraz jakości uzyskiwanych produktów. Istnieje wiele czynników, które należy uwzględnić podczas podejmowania decyzji o zakupie tego typu urządzenia. Przede wszystkim należy określić rodzaj surowców oraz wymagania dotyczące jakości końcowego produktu. Różne typy destylatorów charakteryzują się różnymi parametrami pracy oraz zdolnością do separacji składników, dlatego ważne jest dopasowanie urządzenia do specyfiki procesu technologicznego. Kolejnym istotnym czynnikiem jest wydajność urządzenia oraz jego zdolność do pracy ciągłej lub wsadowej, co ma wpływ na koszty eksploatacji oraz elastyczność produkcji. Należy również zwrócić uwagę na dostępność serwisu oraz części zamiennych dla wybranego modelu destylatora, co ma kluczowe znaczenie dla utrzymania ciągłości produkcji.
Jakie są przyszłe kierunki rozwoju technologii destylacyjnej
Przyszłość technologii destylacyjnej zapowiada się obiecująco dzięki ciągłemu rozwojowi innowacyjnych rozwiązań oraz rosnącemu naciskowi na zrównoważony rozwój i ochronę środowiska. Jednym z głównych kierunków rozwoju będzie dalsza automatyzacja procesów destylacyjnych, co pozwoli na jeszcze lepszą kontrolę nad parametrami pracy urządzeń oraz optymalizację zużycia energii i surowców. W miarę postępu technologicznego coraz większą rolę będą odgrywać systemy sztucznej inteligencji i uczenia maszynowego, które umożliwią prognozowanie zachowań procesów oraz dostosowywanie ustawień w czasie rzeczywistym. Kolejnym ważnym trendem będzie rozwój technologii odzysku ciepła oraz zastosowanie odnawialnych źródeł energii w procesach destylacyjnych, co przyczyni się do zmniejszenia śladu węglowego całej branży. Dodatkowo wzrośnie zainteresowanie ekologicznymi metodami separacji substancji chemicznych, takimi jak ekstrakcja cieczy czy membrany filtracyjne, które mogą stanowić alternatywę dla tradycyjnej destylacji.